The Japanese word Kaizen means continuous improvement activities and is often considered in the limited context of shop-floor improvement activities or on-site issues. The Kaizen concept is now broadly defined to include ongoing improvement involving everyone in the organization.
Kaizen is based on the belief in people’s inherent desire for quality and work. It requires sharing, caring, commitment, and a different kind of leadership based on personal experience and conviction.
The message of Kaizen is that not a day should go by without some improvement being made somewhere in the company.
As an ongoing process, it signifies minor improvements in the status quo due to ongoing efforts. It ensures that there will be continuous improvement for improvement’s sake.
It generates process-oriented and people-oriented thinking toward improving processes and people’s efforts. It is concerned more with the process than with the result. That Kaizen involves everyone in the organization, from top management down to workers on the shop floor, is evident.
Kaizen can be applied to every aspect of everybody’s activities. Employees are involved in Kaizen through suggestion systems and can play a vital role in upgrading standards.
Management actively considers the suggestions and implements most of them (as high as 95% as in the case of Toyota, where about 40,000 workers worldwide provide 1.5 million suggestions a year). Thus, for the Kaizen spirit to survive, management must make conscious efforts to support the personal efforts of every employee. It calls for substantial management commitment of time and effort.
Four Elements of Kaizen
Simply put, Kaizen consists of four elements:
- Plan, Do, Check, and Act (PDCA) Cycle.
- TQM Function and Professional Function.
- Top-down and Bottom-up Coordination.
- Three-dimensional Management
Plan, Do, Check, and Act (PDCA) Cycle
Kaizen/improvement is generated continuously based on the application of the PDCA cycle. The establishment of new standards or revision of existing standards must follow to sustain Kaizen results, thus forming the basis for the next PDCA cycle. New standards must be set up to sustain Kaizen results in the next PDCA cycle.
TQM Function and Professional Function
Kaizen stresses an integration of both functions. Such integration helps in developing an action plan for generating Kaizen because the application of analytical techniques such as the Pareto diagram, histogram, control chart, or fishbone diagram requires professional knowledge and/or experience.
Top-down and Bottom-up Coordination
Vertical coordination needs to be ensured through the direct involvement of all people in the organization. This requires that the roles of top management, middle management, and line employees be clearly defined and carried out, along with unobstructed two-way communication.
Top management will be responsible for setting up corporate policy and goals, policy management/TQM diagnosis, and promotion of employee participation programs.
Middle management will prepare action plans to achieve the top-level policy and goals, undertake routine management, and promote employee participation programs.
Employees will be encouraged to positively participate in “5S activities” (seri, seiton, seiso, seiketsu, and shitsuke), suggestion program, and quality circle (small group) activity.
Three-dimensional Management
This is needed to integrate the three issues mentioned above into the Kaizen structure. Three-dimensional management refers to policy management (top management), departmental management, and cross-functional or inter-departmental management.
The Kaizen Improvement Focuses on the Use of
- Value-added and non-value-added work activities.
- Muda refers to the seven classes of waste- overproduction, delay, transportation, processing, inventory, wasted motion, and defective parts.
- Principles of motion study and the use of cell technology.
- Principles of materials handling and use of one-piece flow.
- Documentation of standard operating procedures.
- The five S’s for workplace organization are five Japanese words that mean proper management (seiko), orderliness (seiton), personal cleanliness (seiketso), cleanup (seiso), and discipline (shitsuke).
- Visual management by means of visual displays that everyone in the plant can use for better communication.
- Just-in-time principles to produce only the units in the right quantities, at the right time, and with the right resources.
- Poka-yoke to prevent or detect errors.
- Team dynamics, which include problem-solving, communication skills, and conflict resolution.
Concept of 5s
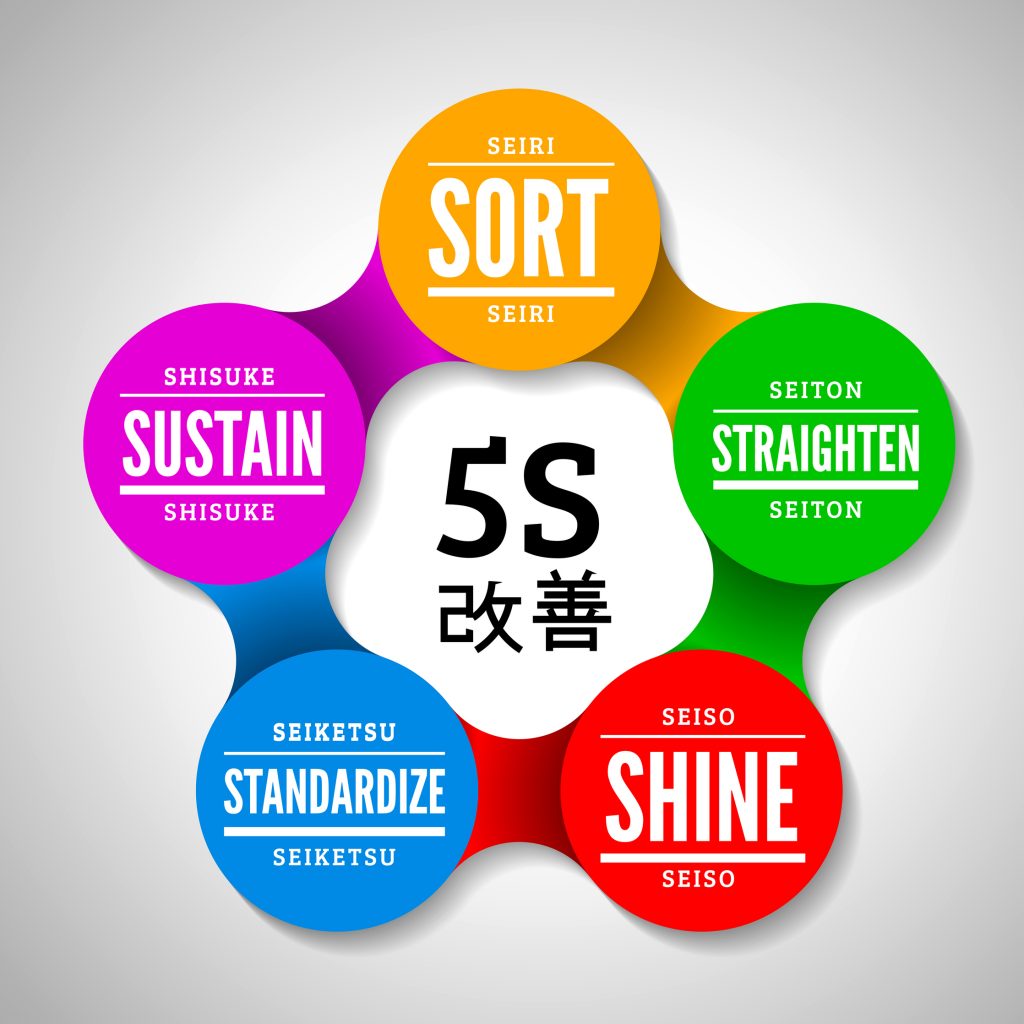
5S is considered an important building block of lean. Its underlying philosophy is that efficient and quality work requires a clean and safe environment.
The 5s activities refer to five Japanese terms such as;
- Seri: sorting out unnecessary items in the workplace and discarding them.
- Seiton: arranging all necessary items to be easily picked for use.
- Seiso: cleaning the workplace completely so that there is no dust on the floor, machines, or equipment.
- Seiketsu: maintaining a high standard of housekeeping and workplace at all times).
- Shitsuki: training people to follow good housekeeping disciplines autonomously).
Briefly, this is a system for organizing the workplace and housekeeping carried out gradually and systematically. The goal of this technique is to create a working environment that is organized, simple, clean, and safe.